Reducing vehicle weight
For lighter, sturdier, and more eco-friendly cars
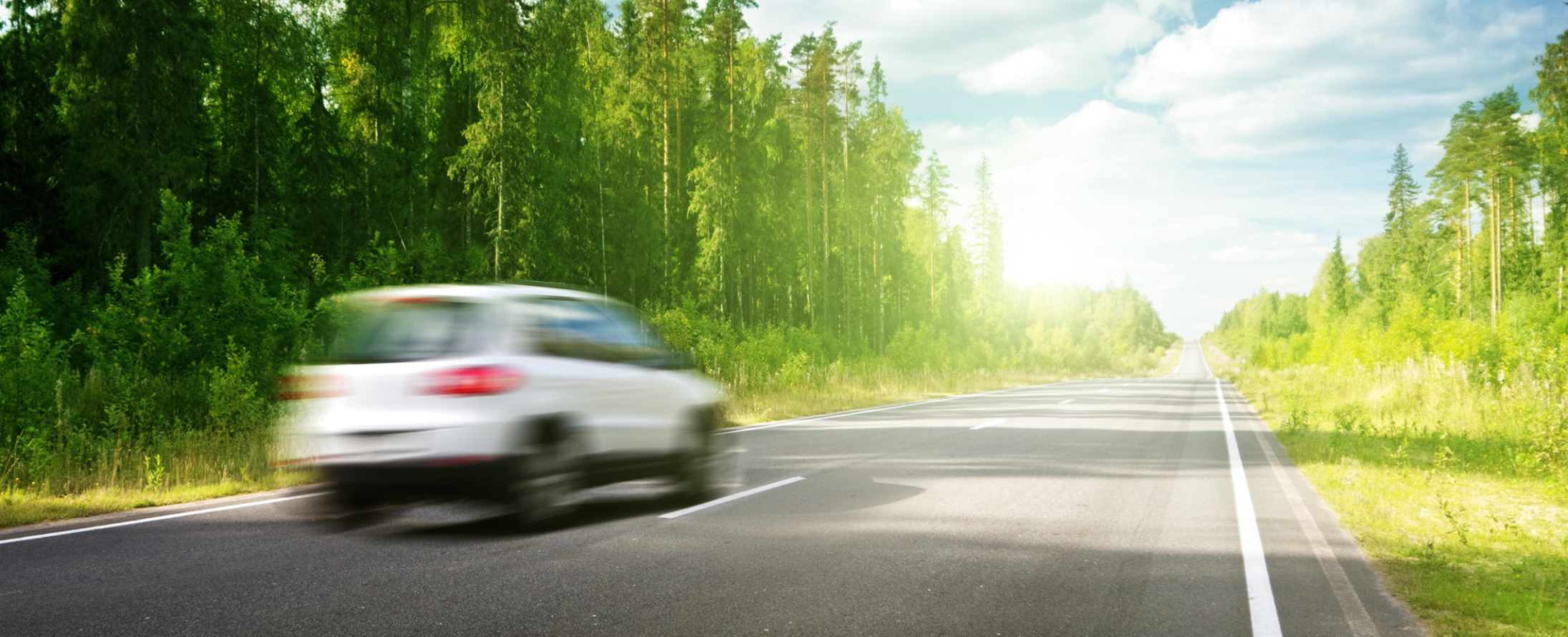
The auto industry has been engaged in the perpetual task of making vehicles lighter, which has a direct effect on improving fuel efficiency and reducing environmental burden. These efforts are becoming increasingly important amid the shift to electric vehicles and stricter environmental regulations. Moriroku Technology has contributed to this evolution of automobiles by applying its extensive expertise in molded plastics to offer solutions for reducing the weight of interior and exterior parts.
Helping vehicles evolve with technology and innovation
Regulations for vehicle exhaust gases and CO2 emissions have been growing stricter every year. In the European Union, automakers are required to reduce the CO2 emissions of new vehicles manufactured from 2021 by 20% compared with current levels. Likewise, the state of California initiated a zero-emission vehicle program and China adopted a new energy vehicle plan. Based on these and other initiatives, exhaust-free electric vehicles along with fuel cell vehicles and environmentally friendly hybrid vehicles must account for certain percentages of all automobiles manufactured and sold.
Accordingly, automobile manufacturers have been making a shift to these types of vehicles from conventional gasoline and diesel fuel vehicles. Furthermore, they have been re-examining the materials used for automobile components, from the frame and body to interior and exterior parts, in an effort to reduce overall vehicle weight. Consequently, manufacturers have been moving to adopt lightweight aluminum and plastic as materials for such parts in place of iron and steel. Nevertheless, iron and steel have merits in terms of cost, rigidity, and strength against collisions, and replacement materials have yet to establish a track record in the auto industry. Therefore, plastic materials face high barriers, and adopting them quickly for all kinds of parts is currently unrealistic.
To overcome this challenge, plastic parts manufacturers must find innovative ways to help realize the cars of the future. Moriroku Technology has been applying proven technologies and creative approaches over many years of developing plastic interior and exterior auto parts, thereby promoting innovation in the auto industry.
Our innovations
Switching to lighter-weight materials
Plastic parts are conventionally made of acrylonitrile butadiene styrene (ABS), which is strong but relatively heavy. To make lighter parts, Moriroku Technology has been using olefin fibers such as polypropylene and mixing them with other materials to compensate for their lack of strength. In Europe, however, manufacturers often use ABS because it can be procured cheaply in the region and they tend to prefer hard materials. Therefore, Moriroku Technology recognizes the importance of selecting materials that are suitable for market needs and customers' requirements.
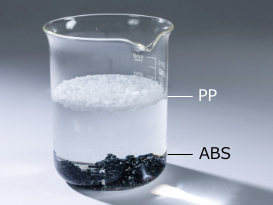
Optimally designing lightweight and strong materials
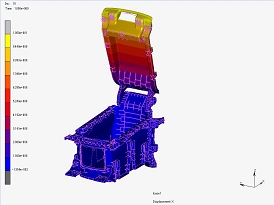
Generally, making materials lighter and thinner also reduces their strength. Nevertheless, Moriroku Technology has succeeded in making parts that are both lightweight and strong by using computer aided engineering (CAE)* to effectively analyze material strength, check the structure of unseen components, and adjust the positions of ribs and flanges. While making sure to meet functional requirements, the company implements innovative methods to optimize designs, such as minimizing materials and integrating parts made up of numerous components.
CAE is a computer technology used in manufacturing R&D to simulate and analyze digital prototypes as an alternative to testing and experimenting on physical prototypes.
Creating innovative new materials
Moriroku Technology is developing and using new carbon fiber materials that offer higher performance and environmental friendliness. Click on the link below for more information.
The Moriroku Group's original solutions
Very few manufacturers completely specialize in interior and exterior auto parts like Moriroku Technology, which is also able to draw from Moriroku Chemicals' trading network and material development technologies. By collaborating, both companies handle every stage of operations, from procuring materials to commercializing products—a major competitive advantage. Furthermore, the Moriroku Group's network of companies and offices in over 50 countries can deliver localized solutions to automakers right at their sites. Leveraging these advantages, Moriroku Technology will work to help accelerate the evolution of automobiles as a partner capable of supplying all interior and exterior parts for a complete vehicle.