Instrument panel module development
Serving as a total supplier of peripheral parts for instrument panels
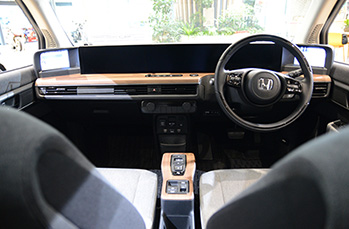
We also place a thorough emphasis on how air-conditioning outlets and other moving parts feel to touch, simultaneously giving them a smooth, gentle movement and a firm clicking sensation.
Combined with our richly-varied decoration technology, such as coating that gives off a sense of softness and warmth, we offer a total lineup of instrument panel parts.
Moriroku's instrument panel module development technology—from design to production
Mold flow and rigidity prediction through CAE analysis
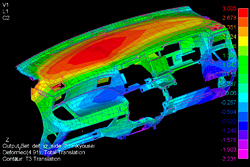
We participate in customer projects from the initial car development stage and build the basic frame structure of the instrument panel based on already developed technology.
In the design phase, we use CAE* to perform molding flow and rigidity predictions, and evaluate the completed prototype for performance using our own test equipment.
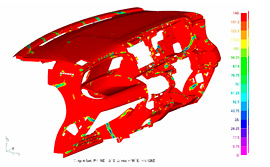
Also, peripheral components (glove compartments, panels, outlets, ducts, etc.) to be integrated into the instrument panel can be developed and designed simultaneously and the assembled instrument panel module delivered.
-
※
CAE is a technology that performs simulation analysis with a prototype simulated on a PC, instead of testing or experimenting with a prototype made of actual materials that is used in the R&D process.
Instrument panel design technology features
Consistent handling of the instrument panel and the parts that are integrated into the panel achieves the following advantages.
-
Minimizes bumps and cracks on the mating surfaces of parts.
-
Standardizes how moving parts (air conditioner vent, etc.) feel when touched or adjusted during operation.
-
Produces a uniform appearance in color, polish, texture, etc.
Nearly all instrument panels by Moriroku
For instance “Compact vehicle”, it was necessary to have an abundant variety at the ready despite limited costs in order to accommodate the needs of a wide-ranging customer base, including veteran drivers downsizing from higher-end models and young individuals who has just acquired their driver’s license.
Moriroku has had a hand in nearly all of the diverse instrument panel parts that went into the customers vehicle.
The image, just one sample of that variety, show how we used synthetic leather and fabric covering on parts found from the compartment lids on the passenger seat side up to the area around the steering wheel. Their soft touch that conveys a small sense of thickness gives the parts a luxury feel, reflecting current trends.