Recycling plastic at manufacturing plants
Effectively using limited raw materials in production
Amid growing awareness of ocean plastic pollution—a global environmental problem—Moriroku understands its responsibilities as a manufacturer of plastic auto parts. Accordingly, the company has been reusing waste plastic generated from its production processes, such as scraps and defective items, as plastic raw materials. Properly separating various kinds of waste plastic is essential for increasing the amount of materials that can be reused in comparison with the amount that is recycled through incineration. Therefore, the company works to ensure that all production plant employees understand correct waste plastic separation, such as by using detailed product classification charts.
Recycling a higher ratio of plastic materials
During plastic product manufacturing, preventing defects such as small scratches and burrs1 is practically impossible. Moriroku treats such defective items as waste plastic for both material and thermal recycling. Since reusing materials is comparatively more environmentally friendly, the company has been carrying out various measures to increase the ratio of material recycling.
Thermal recycling is a method by which waste plastic is incinerated as fuel in boilers or power generators. Moriroku mainly reuses scrap nylon, resins containing glass fibers, and polycarbonate resin for this process, and sends such materials to a specialized company to be processed as refuse-derived fuel2, which is then used by various recycling operators.
Material recycling is a method by which waste plastic is reused as raw materials. The waste that Moriroku reuses is mainly polypropylene and acrylonitrile butadiene styrene (ABS). This waste is first pulverized at its two factories in Japan, the Kanto Plant and Suzuka Plant. Then it is either processed into plastic pellets by a business partner and reused again by the plants as raw materials for manufacturing the same types of plastic, or it is sold to recycling companies that process the waste into recyclable pellets themselves.
Compared with thermal recycling, material recycling has a comparatively lower environmental burden, but the waste plastic must have a high level of purity in order to be reused as a good-quality raw materials for the same types of plastic. Therefore, proper sorting of discarded waste plastic is essential. Accordingly, the company carefully sorts waste to increase the amount that can be used in an effort to increase the material recycling ratio. In practice, however, the plants handle many resin materials that are very similar in appearance, and reusing them for the same types of plastic is difficult if different materials are mixed together in the pulverization and pellet-making processes.
To overcome this difficulty, Moriroku has taken steps to raise awareness of proper waste separation among its employees. For instance, the company has produced detailed product classification charts for helping employees separate and collect waste according to precise criteria for materials, color, and so on, and posted the charts at prominent places at its production plants.
-
*1
Burrs are protrusions and imperfections that can occur during molding when melted resin flows into gaps of molds, and during machining when breakages result from machine operations.
-
*2
Refuse-derived fuel is a high-grade solid fuel made of unrecyclable waste paper and waste plastic.
Separation of waste plastic
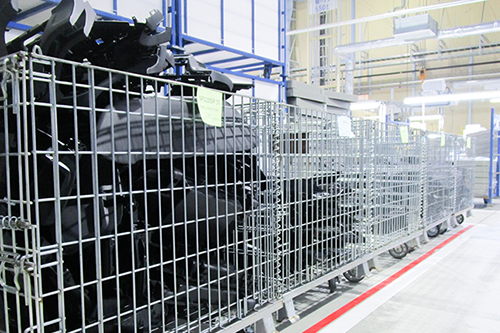
At the Kanto Plant, designated waste plastic collection areas have been set up for separating waste according to three categories: materials not to be pulverized, materials to be pulverized, and materials for thermal recycling.
Facilitating recycling through innovations
Depending on how parts are made, the recyclability of their materials can be improved. For example, the console box of a vehicle (plastic storage compartment between the two front seats) has hinges that are usually made of metal, which must be removed before the plastic materials can be recycled. Therefore, Moriroku offered to manufacture all-plastic console boxes to automakers, which can be crushed and recycled without any additional time and labor for disassembly since the hinges are also made of plastic. Similarly, for an increasing percentage of its parts, the company has been using vibration welding to join components together instead of conventionally used screws and adhesives, as they constitute foreign matter if mixed in with recycled plastic.
As the needs of manufacturers in the auto industry grow more diverse, a greater variety of new materials are needed for parts. To find solutions for the seemingly contradictory tasks of responding to diverse needs and facilitating recycling, Moriroku is pursuing innovations in an effort to both satisfy these manufacturers and deal with environmental issues.